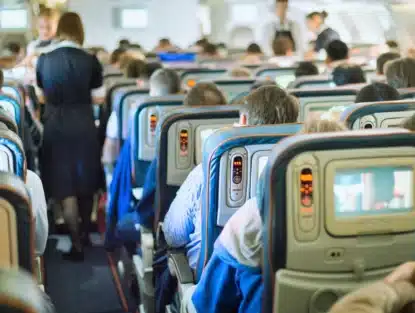
13 Sep, 2016
Turbulence Causes a Wave of Injuries for Flight AttendantsRecent reports reveal that severe turbulence has been responsible for a wave of injuries involving…
Laboratories often use a number of hazardous chemicals. These chemicals are used in the development of products, testing processes and for the cleaning of equipment. Exposure to these chemicals can heighten employees’ risks of developing health issues. To protect Illinois workers from unnecessary occupational diseases, chemical burns and other injury, the Occupational Safety and Health Administration has established strict guidelines for laboratories to follow.
Chemical hygiene plans
When hazardous chemicals are present, laboratories are required by law to draft a written chemical hygiene plan. The plan’s purpose is to monitor every aspect of employee contact with the chemicals and includes the following:
In addition, the plan should also contain the names of the employees responsible for the plan’s implementation. Laboratories are encouraged to establish a chemical hygiene officer and even a committee, if necessary.
Documentation relating to hazardous chemicals
OSHA requires laboratories to collect and retain information as part of its standard relating to hazardous chemicals. For instance, laboratories must keep a record on any employee who is working with, or exposed to, hazardous chemicals. These records include physician opinions, medical tests, exposure monitoring measurements and medical consultation. Laboratories are also required to keep a written record of the chemicals in use.
Employees should also keep documentation of the chemicals that they are exposed to as well as medical records relating to their personal safety. If employees are not receiving written information from their employers, they should request that information and, if necessary, contact OSHA with their concerns. Laboratories found to be ignoring the standard regulations face citations and other penalties from OSHA.
Hazard identification
All hazardous chemicals must be identified as such with labels. The labels need to be in perfect condition for easy reading and contain information that notifies employees of the risks associated with using the chemicals. These risks can include skin corrosion, germ cell mutagenicity, aspiration hazard, acute toxicity, eye damage and respiratory sensitization. If these labels are not present or readable, employees can find themselves unnecessarily at risk for an on-the-job injury.
A material safety data sheet is also required for each chemical considered hazardous. Employees should have access to these sheets which provide important information on how to use and handle the chemicals. The material safety data sheet also includes data on procedures for spills, physical characteristics of the chemicals, personal protective equipment to be used and explosion or fire risks.